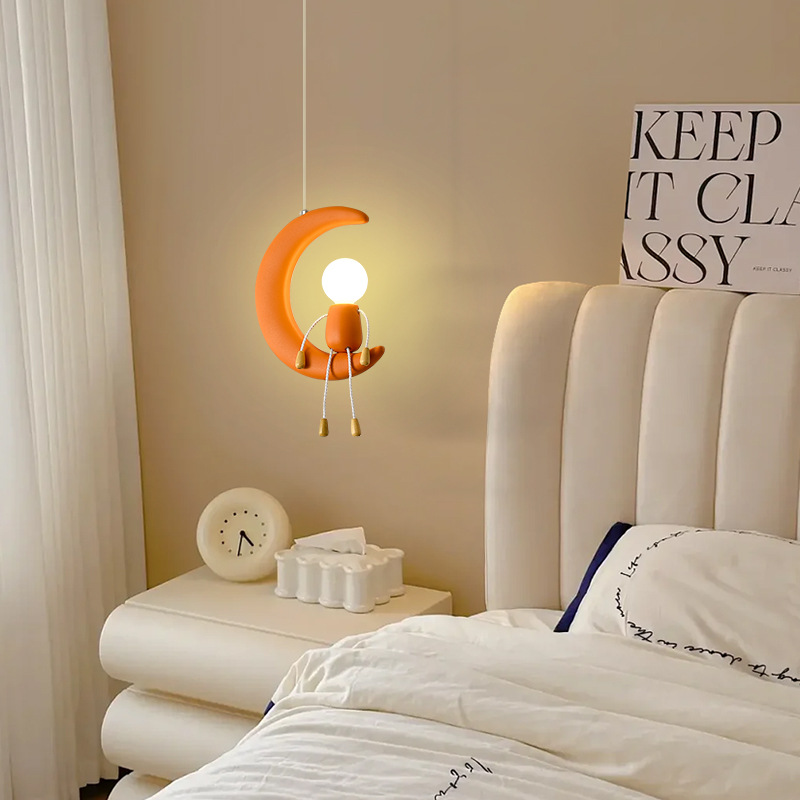
Shining a Light on Creativity: The Art of Crafting an Aluminum Chandelier
Aluminum chandeliers have become increasingly popular in recent years, and it’s not hard to see why. These stunning fixtures add a touch of elegance and sophistication to any space, whether it’s a grand ballroom or a cozy dining room. The beauty of xlightings aluminum chandeliers lies not only in their design, but also in the material itself. Aluminum is a versatile and durable material that lends itself well to chandelier making, making it an excellent choice for both designers and homeowners.
One of the main reasons why aluminum is a great material for chandeliers is its lightweight nature. Unlike other metals such as brass or iron, aluminum is much lighter, making it easier to install and hang from the ceiling. This is especially important when dealing with larger chandeliers that may require multiple people to lift and install. Additionally, aluminum is resistant to corrosion and rust, ensuring that your chandelier will maintain its beauty for years to come. Its malleability also allows for intricate designs and shapes that would be difficult to achieve with other materials.
The History of Aluminum in Chandelier Making
The use of aluminum in chandelier making dates back to the early 20th century. At the time, aluminum was considered a precious metal due to its rarity and high cost of production. However, advancements in technology and manufacturing processes made it more accessible, leading to its use in various industries, including chandelier making.
One famous example of an aluminum chandelier is the one found in the Metropolitan Opera House in New York City. Designed by Jules Bouy and installed in 1966, this stunning chandelier features over 20,000 individual pieces of aluminum suspended from the ceiling. Its intricate design and shimmering appearance make it a true work of art.
Another notable aluminum chandelier is the one found in the Palace of Versailles in France. This chandelier, known as the Hall of Mirrors Chandelier, was created in the 17th century and is made entirely of aluminum. It is a testament to the durability and longevity of aluminum as a material for chandeliers.
The Design Process: From Sketch to Final Product
The design process for aluminum chandeliers begins with a sketch or concept. Designers work closely with clients to understand their vision and requirements for the chandelier. Once the design is finalized, it is translated into a technical drawing that serves as a blueprint for the manufacturing process.
The next step in the design process is creating a prototype or mock-up of the chandelier. This allows designers to test the functionality and aesthetics of the design before moving forward with production. Adjustments and modifications can be made at this stage to ensure that the final product meets the client’s expectations.
Once the prototype is approved, production can begin. This involves sourcing the necessary materials, such as aluminum rods and sheets, as well as any additional components such as crystals or glass shades. The aluminum is then cut, shaped, and assembled according to the design specifications. This may involve welding, soldering, or other techniques to join the pieces together.
Materials Used in Crafting Aluminum Chandeliers
In addition to aluminum, other materials are often used in crafting aluminum chandeliers to enhance their beauty and functionality. These materials include crystals, glass shades, and decorative elements such as beads or pendants.
Crystals are a popular choice for adding sparkle and elegance to chandeliers. They come in various shapes and sizes, and can be arranged in different patterns to create stunning visual effects when illuminated. Glass shades are another common feature in chandeliers, providing a soft and diffused light that adds warmth to any space.
When it comes to decorative elements, designers have endless options to choose from. Beads, pendants, and other ornaments can be added to the chandelier to create a unique and personalized look. These elements can be made from a variety of materials, including glass, metal, or even natural materials such as shells or feathers.
The Role of Lighting in Chandelier Design
Lighting plays a crucial role in chandelier design, as it not only illuminates the space but also enhances the overall aesthetic appeal of the fixture. Different types of lighting can be used in chandeliers to create different effects and moods.
One common type of lighting used in chandeliers is ambient lighting. This provides a general, overall illumination to the space and is often achieved through the use of multiple light bulbs or candles. Ambient lighting creates a warm and inviting atmosphere, making it ideal for dining rooms or living areas.
Another type of lighting used in chandeliers is accent lighting. This involves highlighting specific areas or objects within the space, such as artwork or architectural features. Accent lighting can be achieved through the use of spotlights or directional bulbs that can be adjusted to focus on a particular area.
Finally, there is task lighting, which is used to provide focused illumination for specific tasks such as reading or cooking. Task lighting can be incorporated into chandeliers through the use of adjustable arms or movable shades that can be directed towards the desired area.
Techniques for Crafting and Shaping Aluminum
Crafting and shaping aluminum requires a combination of traditional techniques and modern technology. One common technique used in chandelier making is bending or shaping the aluminum rods or sheets. This can be done using specialized tools such as bending machines or by hand using heat and pressure.
Welding is another technique used to join aluminum pieces together. This involves melting the aluminum at the joint and then allowing it to cool and solidify, creating a strong bond. Soldering is a similar technique that uses a lower melting point material, such as tin or lead, to join the pieces together.
In addition to these techniques, modern technology such as computer-aided design (CAD) and computer numerical control (CNC) machines are also used in the crafting and shaping of aluminum chandeliers. CAD allows designers to create precise and detailed 3D models of the chandelier, which can then be used to guide the manufacturing process. CNC machines, on the other hand, use computer-controlled tools to cut, shape, and drill the aluminum with high precision and accuracy.
The Importance of Precision in Chandelier Making
Precision is of utmost importance in chandelier making, as even the smallest deviation can affect the overall appearance and functionality of the fixture. This is especially true when it comes to the alignment of the crystals or glass shades, as any misalignment can create a distracting or unbalanced look.
To ensure precision, chandelier makers use a variety of techniques and tools. One common technique is measuring and marking, where precise measurements are taken and marked on the aluminum before cutting or shaping. This ensures that each piece is cut to the correct size and shape.
Another technique is jigging, which involves using a jig or template to guide the shaping or assembly process. Jigs are often made from wood or metal and are designed to hold the aluminum pieces in place while they are being worked on. This helps to ensure that each piece is positioned correctly and consistently.
Finally, quality control checks are conducted throughout the manufacturing process to ensure that each chandelier meets the required standards of precision. This may involve visual inspections, measurements, or functional tests to ensure that all components are properly aligned and functioning as intended.
Finishing Touches: Polishing, Painting, and More
The finishing touches are what truly bring an aluminum chandelier to life. These include polishing, painting, and other decorative techniques that enhance the beauty and durability of the fixture.
Polishing is an important step in the finishing process, as it removes any imperfections or blemishes on the surface of the aluminum. This can be done using specialized polishing compounds and tools, such as buffing wheels or sandpaper. The goal is to achieve a smooth and reflective surface that enhances the overall appearance of the chandelier.
Painting is another option for adding color and texture to an aluminum chandelier. This can be done using a variety of techniques, such as spray painting or hand-painting. The choice of paint will depend on the desired finish and durability, with options ranging from metallic finishes to matte or glossy colors.
Other decorative techniques that can be used in the finishing process include gilding, where a thin layer of gold or other precious metal is applied to the surface of the chandelier, and patination, which involves applying chemicals to create an aged or weathered look. These techniques add depth and character to the chandelier, making it a truly unique and personalized piece.
Installing and Maintaining Aluminum Chandeliers
Installing an aluminum chandelier requires careful planning and consideration. The weight and size of the chandelier must be taken into account, as well as the structural integrity of the ceiling or support system. It is recommended to hire a professional electrician or contractor to ensure that the installation is done safely and correctly.
Once installed, aluminum chandeliers require regular maintenance to keep them looking their best. This includes dusting or cleaning the fixture regularly to remove any dirt or debris that may accumulate over time. It is important to use gentle cleaning methods and avoid abrasive materials that could scratch or damage the aluminum.
In addition to regular cleaning, it is also important to check the electrical components of the chandelier periodically. This includes inspecting the wiring, sockets, and bulbs for any signs of wear or damage. Any faulty components should be replaced immediately to prevent electrical hazards.
The Future of Aluminum Chandelier Design and Innovation
The future of aluminum chandelier design and innovation looks promising, with new technology and techniques constantly being developed. One area of innovation is the use of LED lighting in chandeliers. LED lights are energy-efficient, long-lasting, and can be programmed to create different lighting effects and colors. This opens up new possibilities for designers to create dynamic and interactive chandeliers that can change with the mood or occasion.
Another area of innovation is the use of 3D printing in chandelier making. 3D printing allows designers to create complex and intricate shapes that would be difficult or impossible to achieve using traditional manufacturing methods. This technology also allows for customization and personalization, as each chandelier can be tailored to the client’s specific needs and preferences.
Overall, the future of aluminum chandelier design and innovation is bright. With advancements in technology and a growing demand for unique and personalized lighting fixtures, we can expect to see even more stunning and innovative aluminum chandeliers in the years to come. Whether it’s a classic design or a modern masterpiece, aluminum chandeliers will continue to captivate and inspire with their beauty and craftsmanship.